Устройство и принцип работы станка для лазерной резки металла
Обработку металла человек освоил в первобытные времена. Ранние века цивилизации названы в честь химических элементов, перевернувших историю — меди и железа, затем началась эпоха первого известного сплава — бронзы. Кузнечное искусство живёт много тысячелетий, в Древнем Риме создавались примитивные, но надёжные сварочные швы, а металлические изделия времён фараонов удивляют отличной сохранностью, высоким качеством и не всегда понятными нам технологиями.
Но лазерная резка металла появилась в арсенале мастеров лишь в середине ХХ столетия, одновременно с освоением космоса. Точнее, первые разработки относятся к 1960 году, а вот полноценная лазерная резка металла была проведена уже в те годы, когда спутники и ракеты перестали удивлять человечество. Разработка универсального оборудования возникла не на пустом месте — были использованы концепции Эйнштейна начала века.
Первый лазер создал физик-теоретик Майман, используя синтетический рубин с зеркальным серебряным покрытием. В 1967 году были проведены работы с помощью лазерного станка, а спустя несколько лет началось их медленное внедрение в производство. Причина паузы — высокая стоимость первых станков, их низкая мощность и огромное потребление электроэнергии.
На промышленный уровень этот метод вышел только к третьему тысячелетию. Революционным стало создание насадки. Изобрёл её Хулдкрофт, обеспечив подачу кислорода для облегчения резки — скорость обработки стального листа при этой технологии достигла метра в минуту при толщине металла 2,5 мм.
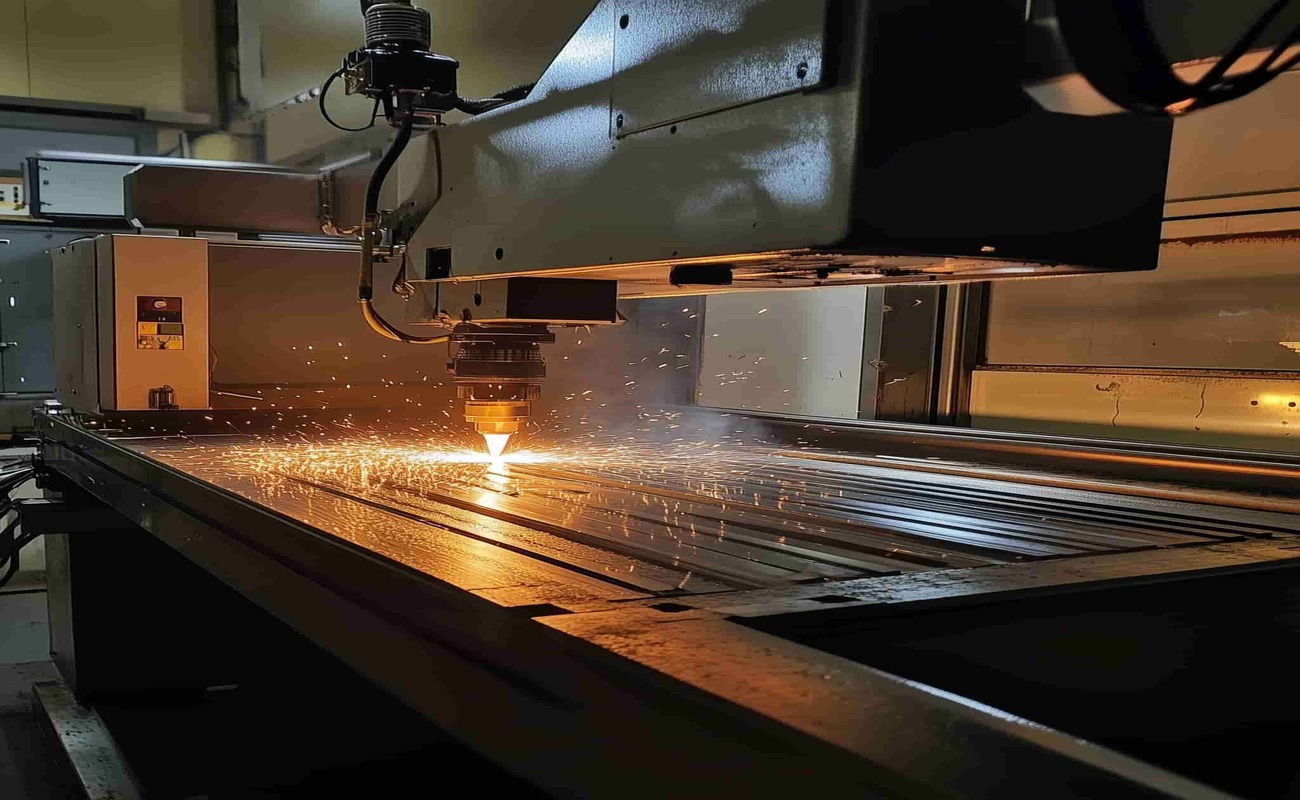
Какие существуют сегодня лазерные станки
Лазер «работает» с различными материалами. Но именно резка металлов сегодня востребована практически во всех производственных областях. В зависимости от обрабатываемого материала и технологической задачи используются несколько видов станков. Большинство моделей предназначено для раскроя листов в автоматическом режиме — станки работают с металлом различной толщины, обеспечивают точность и скорость резки.
Основные типы оборудования:
- CO2-лазеры в редких случаях могут работать и с металлами (если на их поверхность нанесена термопаста), но основная их задача — обработка с высокой скоростью пластика, стекла, дерева, резины и других неметаллов. Выполняют не только резку, но и гравировку, тонкую сварку.
- Оптоволоконные — с минимальными операционными расходами и максимальной точностью обеспечивают обработку металлов и отражающих материалов. Основные характеристики — низкое энергопотребление и беспроблемное обслуживание. Подходят для большинства металлов и сплавов — от резки стали до серебра, от латуни до меди. Не используются для работы с неметаллами.
- Волоконные лазеры и Nd:YAG. Область применения — керамика и металлы, в том числе отражающие и тугоплавкие.
- Ультрафиолетовое оборудование — работает без прямого контакта. Используется для маркировки, гравировки и микрообработки с высокой точностью.
Оптимальный тип станка определяется не только по обрабатываемому материалу, но и целому комплексу критериев:
- сложность задач;
- толщина материала;
- скорость операции;
- размер деталей;
- зона обработки;
- объём производства.
Из чего состоит и как действует лазерный станок с ЧПУ
На обрабатываемую деталь направлен высокотемпературный луч, который выжигает поверхность. В зависимости от настройки станка, он может выполнить сквозной рез или снять поверхностный слой.
Несмотря на различие конструкций и задач, устройство большинство лазерных станков включает в свою схему:
- Излучатель — это может быть твердотельный или газовый лазер, а также генерирующий луч.
- Координатное устройство — двигатель + привод + исполнительные механизмы. Его задача — обеспечить перемещение лазерного луча.
- Датчики, входящие в единую систему автоматизированного управления.
- Система, которая готовит газовый состав и выводит его к месту реза.
- Система фокусировки, дополненная юстировочным лазером, поворотными зеркалами и оптикой.
- Стабилизатор напряжения.
- Чиллер — его параметры зависят от мощности лазера.
Поскольку конечная задача лазерного оборудования схожа с работой фрезеровочных станков, многие модели имеют и внешнее сходство. В первую очередь это относится к оборудованию для работы с плоским прокатом. Более сложная конструкция у станков для резки труб и профилей. Основное отличие от фрезы — лазер действует бесконтактным способом.
Важно: любой контактный способ резки подразумевает появление стружки, иных механических отходов. Лазерная обработка означает, что лишний материал «испаряется» — происходит изменение его структуры.
Отличия от других методов резки
Помимо технических преимуществ (точность, оперативность), лазерная резка означает и финансовое преимущество — даже в том случае, если речь идёт о небольшой партии заготовок.
Основные плюсы резки с использованием лазерного оборудования:
- скорость работы даже при больших объёмах производства;
- возможность создать пропил (рез) минимального диаметра;
- незначительное коробление;
- широкий диапазон толщины обрабатываемого металла, включая изделия менее 0,1 мм;
- точность значительно выше, чем при плазменной и газовой резке;
- работа как с 2-х, так и с 3-х мерными заготовками;
- беспроблемное выполнение резки или гравировки сложной конфигурации;
- простота настройки параметров станка;
- гибкость — не требуется постоянная смена инструмента для выполнения различных задач.
После лазерной резки детали не нуждаются в дополнительной обработке. Если верно подобраны и установлены параметры, то лазерный станок без проблем справляется с хрупкими материалами и заготовками, которые могут деформироваться при других видах резки.
Модели станков с ЧПУ включают в конструкцию контроллер, который позволяет выставить все необходимые характеристики обработки материала. Его задачи:
- Регулировка частоты вращения инструментов и подвижных элементов станка.
- Смена инструмента.
- Обеспечение зажима заготовки.
- Настройка точности.
- Корректировка действий инструмента.
Лазерные станки без проблем интегрируются в уже действующие производственные схемы, не требуя их серьёзной модернизации.
С какими задачами справляются лазерные станки
Резка, сварка и гравировка — это общие задачи для лазерного оборудования. Конкретный алгоритм работ зависит от назначения детали:
- изготовление элементов строительной конструкции;
- производство сувениров;
- создание интерьерного декора;
- штамповка указателей и табличек;
- работа над компонентами электротехнических устройств.
Производственные сферы, для которых требуется лазерная резка, различны — от судостроения до автомобильной промышленности, от работы с сельхозтехникой до строительства. Различные модели станков используются в аэрокосмической отрасли и горнодобывающей индустрии.
Немного о гравировке
При этом методе погрешность изображения не превышает 0,01 мм. За одну секунду наносятся десятки точек. Лазерная гравировка имеет дополнительные преимущества:
- Создание сложных изображений.
- Работа с 3D-эффектом.
- Точность конфигурации.
- Долговечность гравировки.
- Возможность нанесения сверхтонких линий.
- Прорисовка мелких деталей.
- Минимальный температурный режим, гарантирующий сохранность материала.
Отсутствие контакта предотвращает деформацию материалов. Не потребуются и дополнительные расходники: никаких химических красителей, штампов, чернил. Возможно создавать многослойные изображения, маркировать медицинские инструменты и выполнять гравировку на космическом оборудовании.
Похожие статьи
Технология, предусматривающая применение лазерной резки, весьма востребована в ряде отраслей, в силу свойственных ей оптимальных соотношений стоимости выполняемых работ и получаемого качества обработки, значительной точности, с которой можно разрезать материал, независимо от объёма изготавливаемой партии товара (от одного изделия).